Benefits of Infrared Thermography
Fix Before Fail
Infrared inspections provide a means to view electrical systems under normal operating conditions to identify abnormally hot areas or components. This is a powerful maintenance tool. In many instances, electrical system failure is preceded by a period of increasing heat.
With infrared thermography you can identify overheating electrical connections, scheduling repairs to be made during planned downtime. This increases reliability and productivity for the entire operation.
Financial Savings
- Fewer interruptions while in operation mean more uptime and greater productivity.
- Problems are fixed before failure which can result in system and machine damage.
- Identifying developing problems and planning the repairs results in fewer “panic situations”, those costly predicaments that force excessive overtime and monetary premiums for emergency rush equipment orders.
Safety
- An industrial process that runs reliably and without surprises produces a safer work environment. Many industrial processes are complex and run at high speed. A sudden failure in one area can have a cascading effect of failures.
- Fire avoidance. Overheated electrical connections can start fires. You may have heard of a fire in your area that it was caused by “faulty wiring.” This means many things including bad design and overloaded circuits. It also commonly means a bad electrical connection that was overheating and was not found in time.
Quality
- A process that runs reliably will produce a higher quality, consistent result compared to one that experiences sudden stops, power failures, and a lack of maintenance to key components.
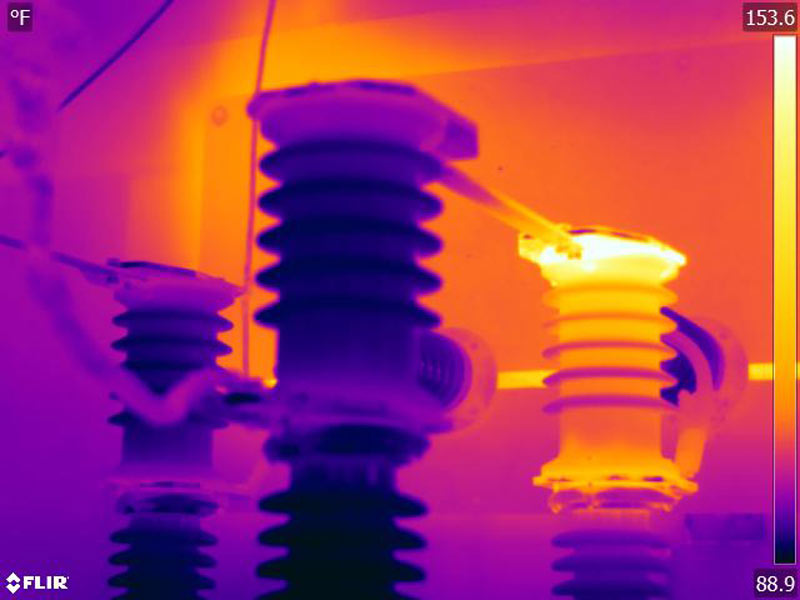
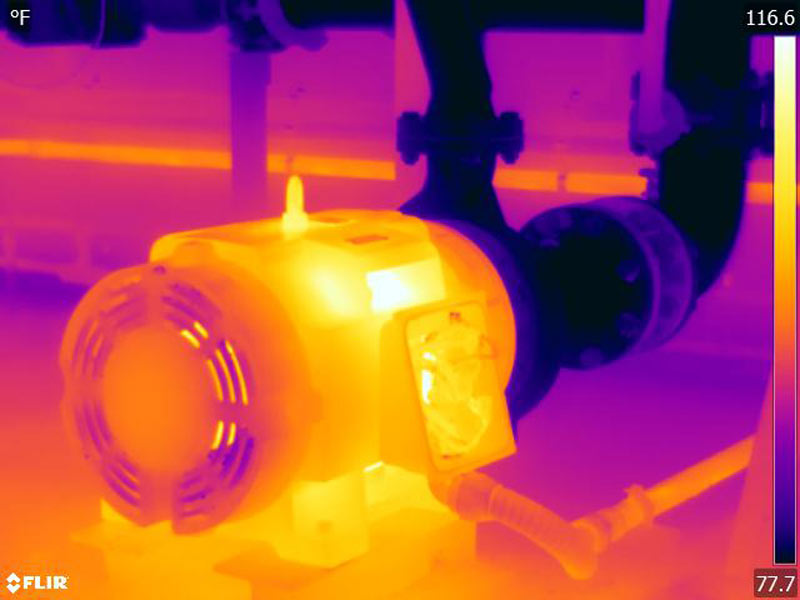
Stop Problems
Before They Start
If the temperature difference is due to a hot electrical connection or abnormal friction, then a problem exists and will only get worse over time. If left to deteriorate on its own the “hot spot” will eventually fail in service with unwanted consequences, ranging from expensive down time and ruined equipment, to electrical fires, panic situations, and worse.